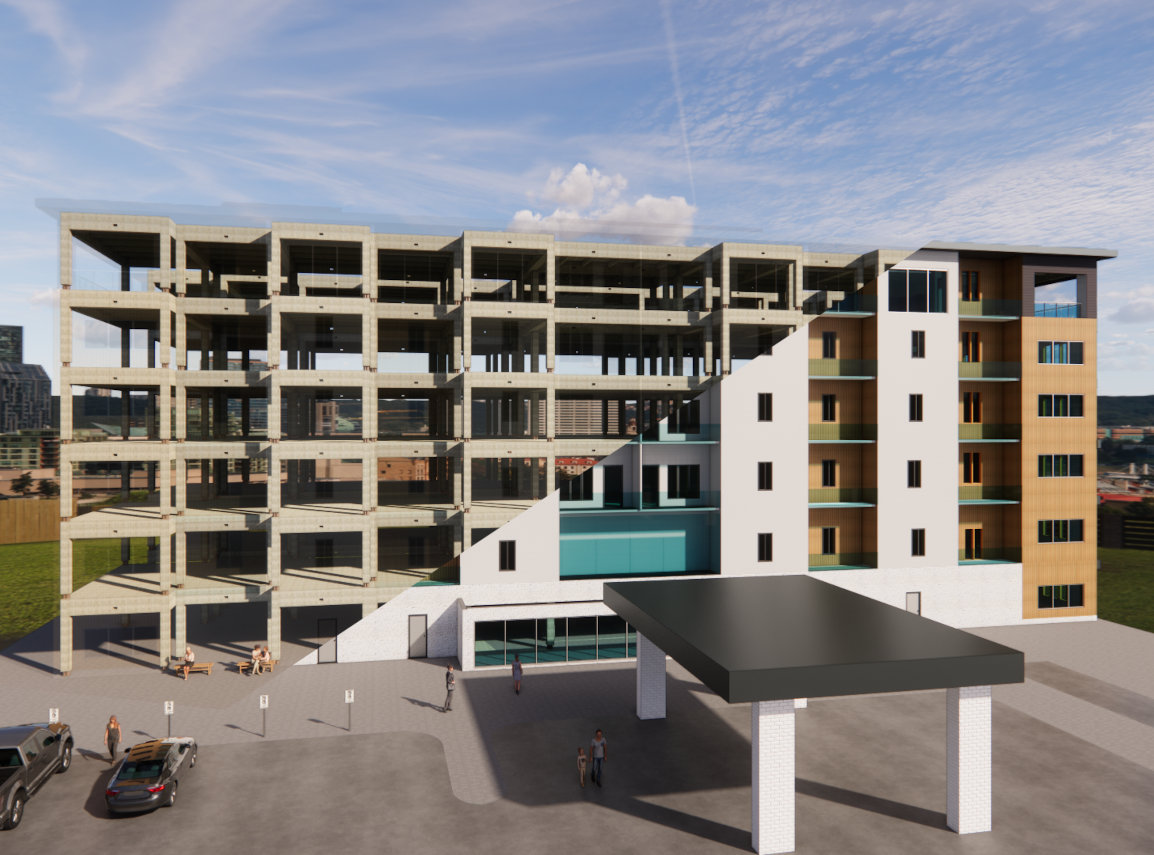
A Better Way to Build
Architects and builders agree, building with Lodestar modules reduces construction time and provides a safe, comfortable, and secure structure. If you’re planning to build a home, office, retail facility, or other structures, efficiency and cost of ownership are important factors to consider. Learn how Lodestar modules provide the best building solution available, making the process quick and effective without compromising quality or comfort.
Designed to Last
Concrete is the primary building material used to construct structures that require strength, durability, and sustainability. Lodestar modules harness the strength of concrete and deliver it to the construction site in a modular package.
Lodestar modules provide an immediate building infrastructure to support all types of building designs and functionality. Available to markets who previously did not have access to a building material solution of this type.
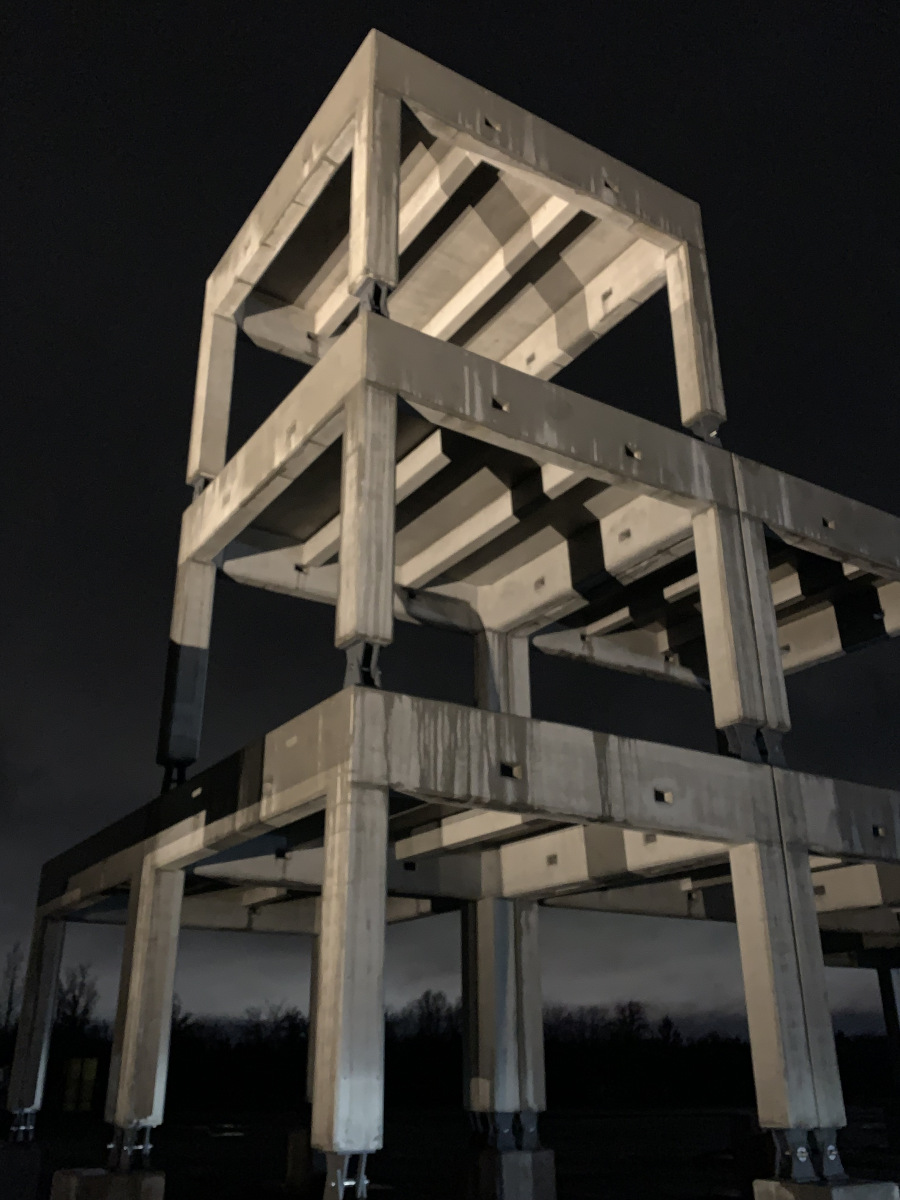
Frequently Asked Questions
Lodestar modular building units are designed to be connected horizontally and vertically, in a modular nature, allowing for an unlimited layout options. The first-floor units are secured to footings, while upper level units are connected to the modules beneath them leveraging the features of the supporting unit(s).
No. The modules reduce construction framing time buy as much as 75%, and overall construction time by up to 50%. The modules are manufactured year-round in a climate-controlled facility, allowing them to be delivered to the site on specific dates and immediately placement. This systematic process allows the builder to focus on enclosing the structures and focusing more time on completing the interior of the building. Enclosing the building in a shorter period allows builders to complete projects that would otherwise be scheduled around seasonal weather and severe weather events.
The Lodestar modular building units do not require the use of specific material or building methods.
Our modules are designed to accept prefabricated wall cladding, windows and doors, and to accept a variety of building materials or methods to enclose the structure. The modular building units are designed with threaded wall anchor inserts on vertical surfaces, allowing you to connect modular wall cladding or have a builder enclose the units using a building method of your choice.
The modular structures have been approved for residential applications up to 7 levels (for a project in Kingston Ontario Canada). There is no limit to the number of modular building units that can be connected horizontally. Regional building codes should be investigated and adhered to.
Certified builders have been trained and experienced with the process of installing the modular building units, however due to the simplified installation requirements most builders and contractors would be able to follow the installation blueprints and effectively install modular building units. If additional information or support is required, our team of experts is available to provide knowledge, support, and information to ensure the builder understands how to complete the project.
The modules are designed at a direct 2 to 1 ratio, allowing contractors and designers to use either of the two sizes to build a floorplan layout that meets the needs of the occupant. The 2 to 1 ratio allows you to use two MBU-218 to create the same layout as one MBU-436. If your location prevents you from transporting or hoisting the MBU-436, you can simply connect two MBU-218 to create the same footprint, with no space or layout compromise.
Lodestar modular building units were designed to achieve maximum transportation efficiency on a variety of roads and highways. The delivery range has been set based on a cost efficiency calculation. The delivery area generally includes locations within 100KM from Kingston, Ontario. Some locations may require special planning, please contact us directly to confirm delivery is available.
Our modular building units are designed to be transported on most major roadways without the need for specialty permits and with traditional planning. The transportation trailer is outfitted with a custom support system that securely carries the module from the storage location to the building site. The module can be lowered from the trailer using the built in hydraulic system, can be hoisted from the trailer directly into place, or can be stored at the building site for future installation.
Our modular building units have been carefully designed with a forward-thinking approach, allowing the builder to accommodate standard and advanced utility systems. Each unit is designed with a cavity in the ceiling area, allowing for services to be installed and concealed. The modules have aligning utility ports which allow services to be transferred between modules without the need for excessive re-working.
Yes. Lodestar modular building units are intentionally designed to incorporate traditional building styles and methods, in a hybrid fashion. You can construct a wood frame section of the building on the roof of a modular building unit or you could build horizontally using the modular building unit as a primary support frame, adding other framing methods affixed to the unit.
Yes. All modular building units can be connected vertically or horizontally to create the desired layout. There are requirements as to how the modular building units are connected to ensure structural integrity and to allow access ports to line up. The dimensions of the MBU-218 is exactly half of the dimensions of the MBU-436, which serves the purpose of allowing builders to connect 2 X MBU-218’s together to create the same footprint as one MBU-436. This benefit also allows for add-on structures to be connected, vertically or horizontally, to the primary building in later years, if the need for additional space is required.
Absolutely, the modules are the ideal sizes for building tiny houses, starter homes, hobby and recreational buildings, outbuildings, shelters, and so many more applications.
Absolutely, the modules are ideal for building garages, hobby and recreational buildings, outbuildings, shelters, and so many more applications.
Absolutely, the modules are the ideal sizes for building tertiary suites, tiny homes, starter homes, hobby and recreational buildings, outbuildings, shelters, and so many more applications.
Yes, the modules are weather resistant and can be stored in extreme weather conditions without compromising the integrity. The modular building units are built to exact specifications and are built to connect to each other in a modular manner, allowing builders to store the units on site and use them as required. Modular building units are built to connect to other modular building units without having to match specific units together.
Licensed and approved manufactures can produce Lodestar modules in their factories for delivery to their market region. Delivery regions will vary, search for approved manufacturers in the Partners section on our website, contact your local approved manufacture to confirm availability in your area. In many cases orders can be scheduled for future dated deliveries, ensuring builders can rely on inventory being delivered in a timely manner. A benefit of producing the modular building units in a climate-controlled facility is the ability to produce high quality finished products every month of the year regardless of seasonal weather conditions.
The modules are available in two sizes. Careful consideration was used in the design plans to maximize the effectiveness of the capabilities related to the size offerings, while maximizing transportation, manufacturing, and delivery efficiencies.
The two sizes allow a high volume of design flexibility, due to the standardization of the support pillars, allowing for simplified installation while maintaining maximum structural integrity. If additional height is required, the first-floor units can be installed on elevated footings, allowing commercial, retail, hospitality, residential, and other spaces to achieve the desired interior height.
In most cases, yes you can add modular building units to expand existing buildings constructed of traditional building materials. A common application incorporating Lodestar modules is known as a hybrid-structure, which combines Lodestar modules with traditional building material to expand the variety of design features.
The requirement to add modular building units to an existing structure is to prepare required foundation and footings for the units to be positioned. The modular building units can be connected vertically to add multi-level additions adjacent to existing structures. Local building codes should be investigated to confirm the requirements and to acquire necessary building permits.
Planning Resources
Resources are available to help you design and plan your construction project. If you require additional information, we are available to provide additional resources.
Product Specifications
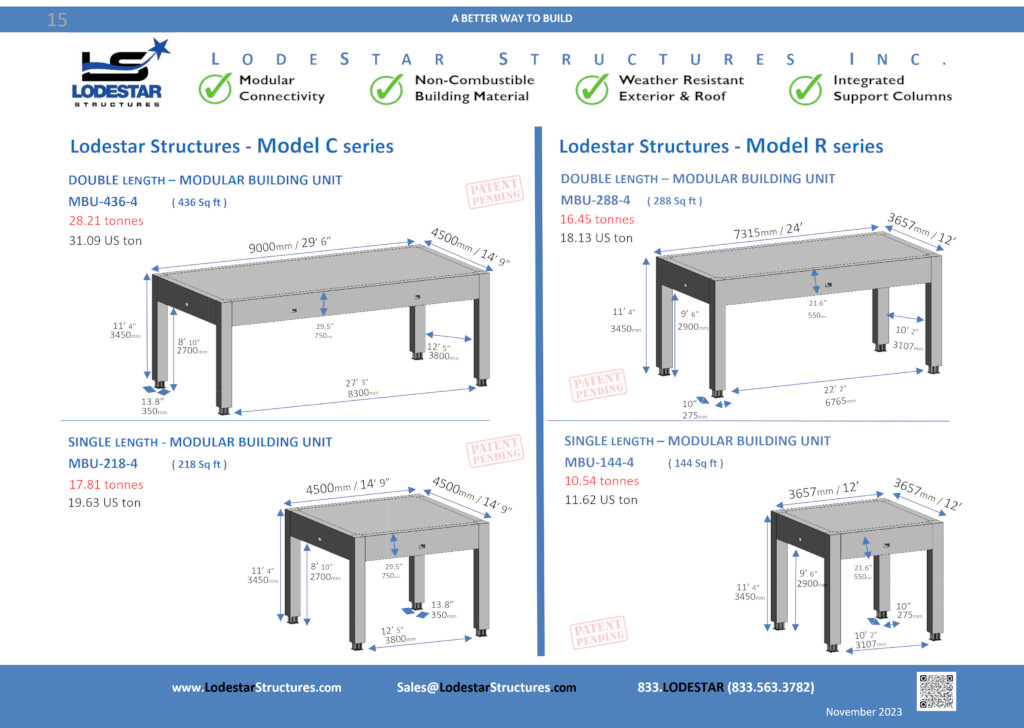
Product Assembly
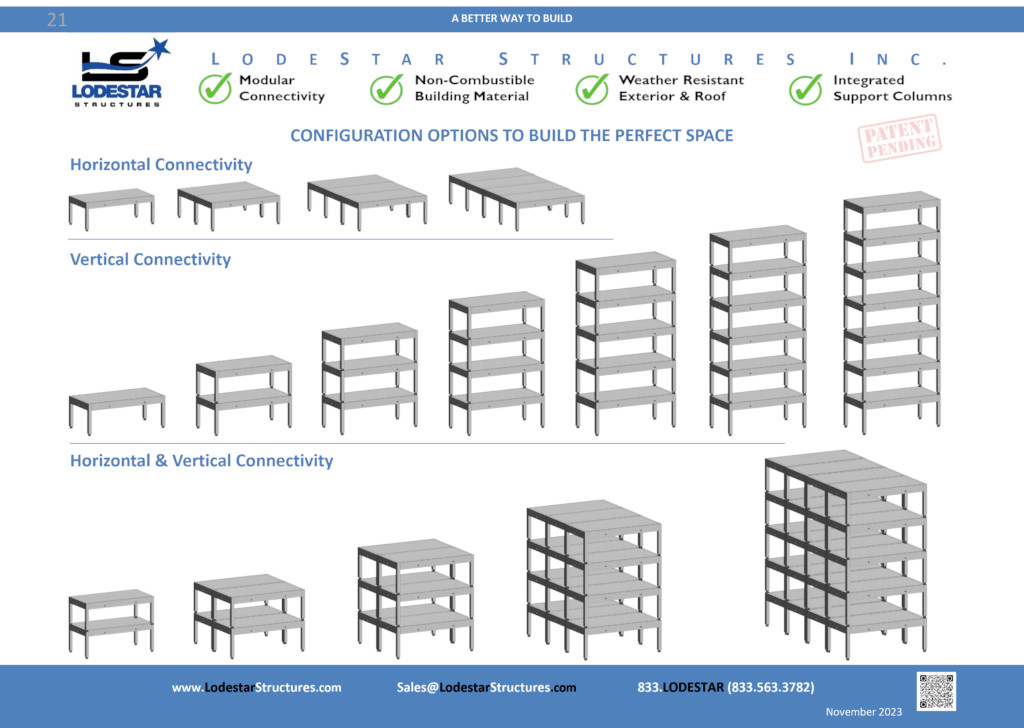
Product Use Illustration
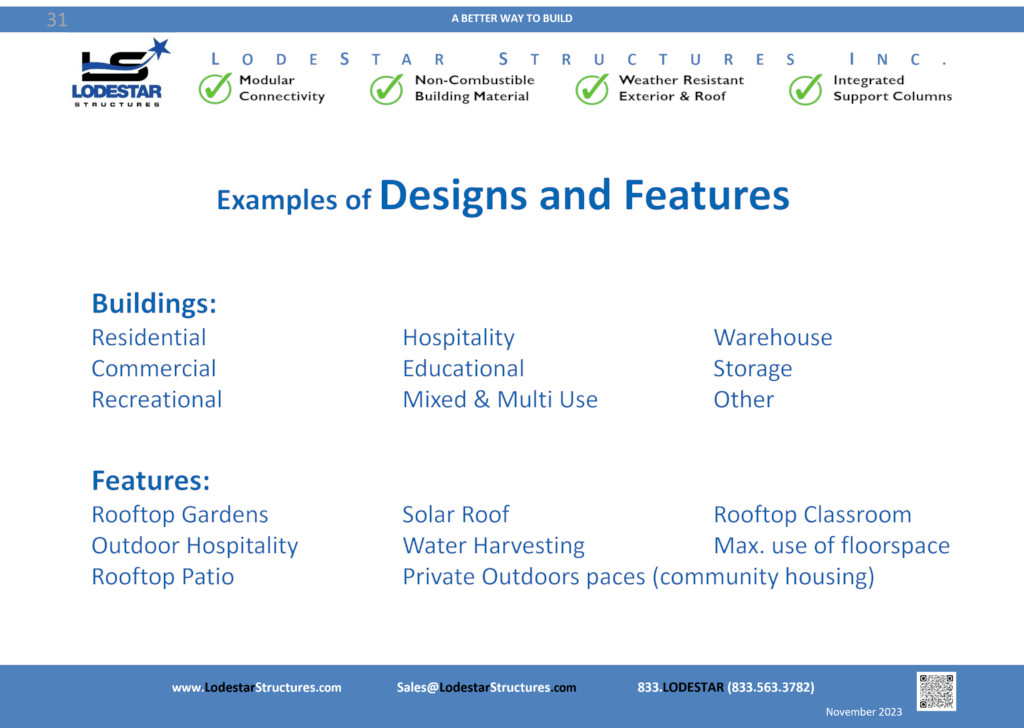
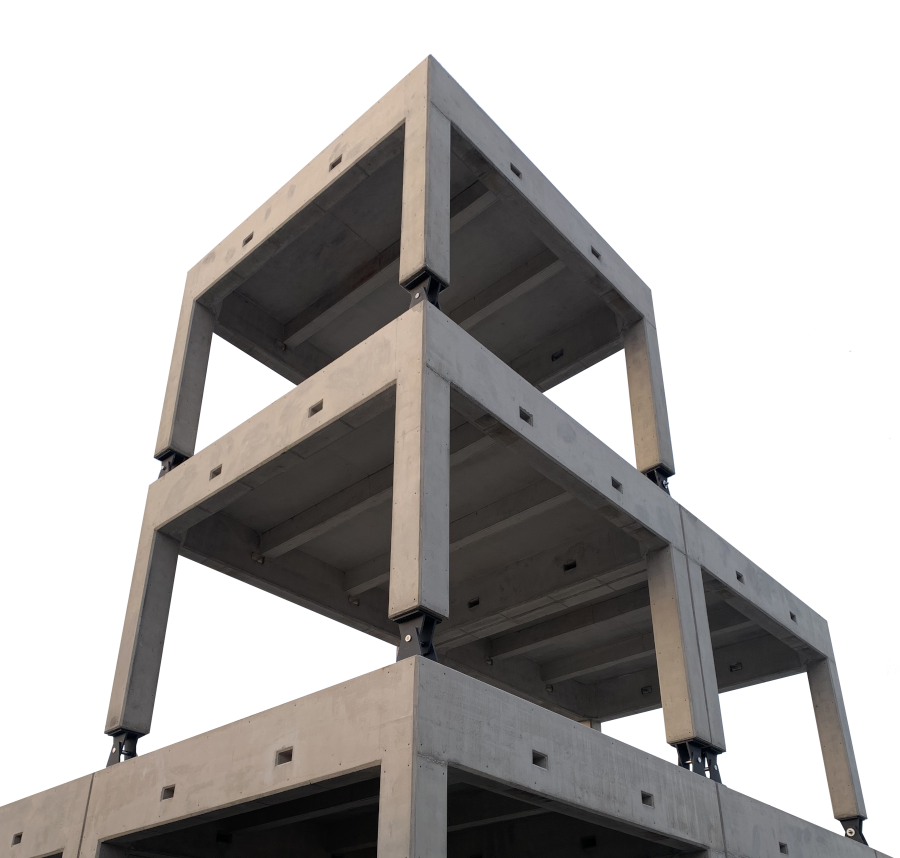
Contact Us
Contact Lodestar or a Lodestar Preferred Partner to learn more about how you can create your perfect space, with Lodestar Building Systems.
Tel: 1-833-563-3782
Email: info@LodestarStructures.com